SINGLE AND MULTI-LANE STRAND FURNACES
Carbolite Gero can supply units to process a single strand. However, for cost efficient production furnaces with up to eight lanes are offered as standard and additional lanes can be added (up to a maximum of 22).
The furnace length is determined by the throughput requirement. The strand passes through Inconel or ceramic tubes and, where required, under the appropriate atmosphere and water cooling (for controlled hardening). A burn-off flame on each tube ensures complete combustion of exhaust gases. Long life wire heating elements are wound around ceramic tubes and are located in both furnace halves. Individually controlled zones provide excellent temperature uniformity which is especially important when heating long lengths.
Depending on tube length and customer requirement, Carbolite Gero can supply a variety of tube supports and tube tensioning systems which ensure the work tubes remain straight. A hinged furnace top allows ease of servicing and cleaning. Low thermal mass insulation ensures fast heat up rates and excellent thermal efficiency. Carbolite Gero offers controls for inert and reactive gases such as cracked ammonia and hydrogen.
CARBOLITE GERO CUSTOM FURNACES & OVENS EXAMPLES
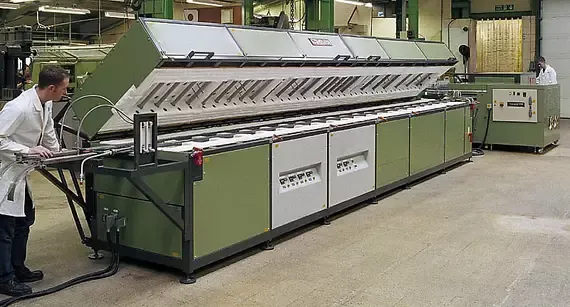
Continuous six-zone strand line for heating stainless steel for a specialist razor blade manufacturer. Two strands are processed simultaneously at up to 15 metres/minute. Separate gas control for cracked ammonia for each lane. After hardening, the strips pass through a water-cooled quench before being tempered.
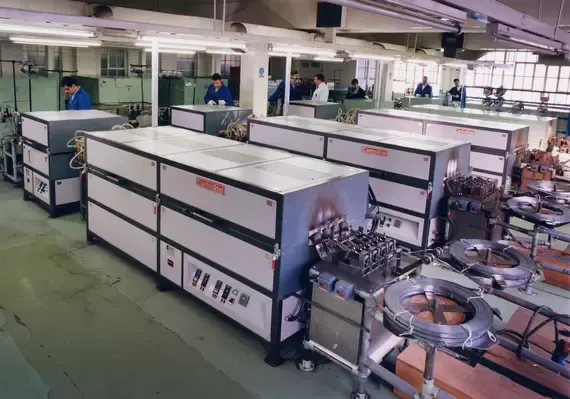
Seven continuous hardening & tempering blade strip line for surgical blades. Each unit has four lanes for heating in hydrogen and then water quenching, before being reheated to achieve tempering.
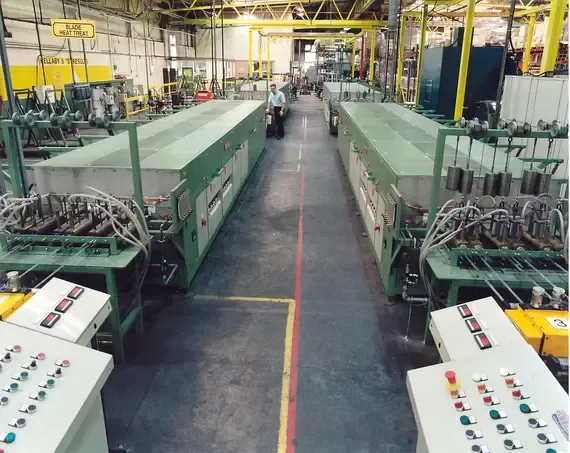
Continuous 6 lane horizontal strand hardening and tempering furnaces under cracked ammonia. Six heated zones in the hardening unit and 9 zones in the tempering unit (3 heated sections with 3 zones)
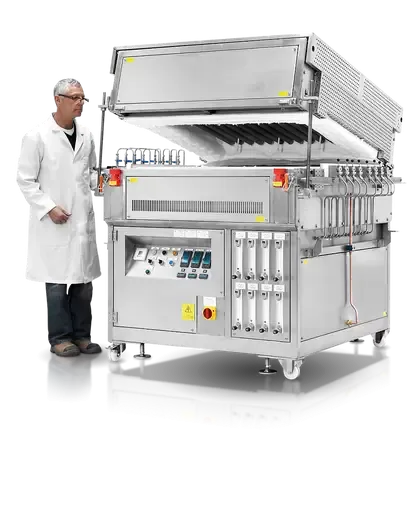
Custom made eight lane strand furnace up to 1300°C with inert gas control