Digitally Controlled Lab Unit for Small Sample Sizes
This pneumatically driven Microfluidizer® processor, with its modern user interface, is designed for the budget-conscious researcher working with small samples.
The LM10 efficiently converts fluid pressure into shear forces. By maintaining constant pressure, this processor ensures that 100% of the material gets exactly the same treatment. And, like all Microfluidizer® processors, the LM10 is unmatched in submicron size reduction, cell disruption and guaranteed process scale-up.
The LM10 Microfluidizer® processor features an economical air-driven intensifier pump that supplies the desired pressure at a constant rate to the product stream. The pump travels through its pressure stroke, driving the product at a constant pressure through precisely defined fixed-geometry microchannels within the Interaction Chamber™.
The product stream accelerates to high velocities, creating shear rates within the product stream that are orders of magnitude greater than any other conventional means. The entire product experiences identical processing conditions, producing the desired results, including uniform product and droplet size reduction (often submicron), deagglomeration and high-yield cell disruption.
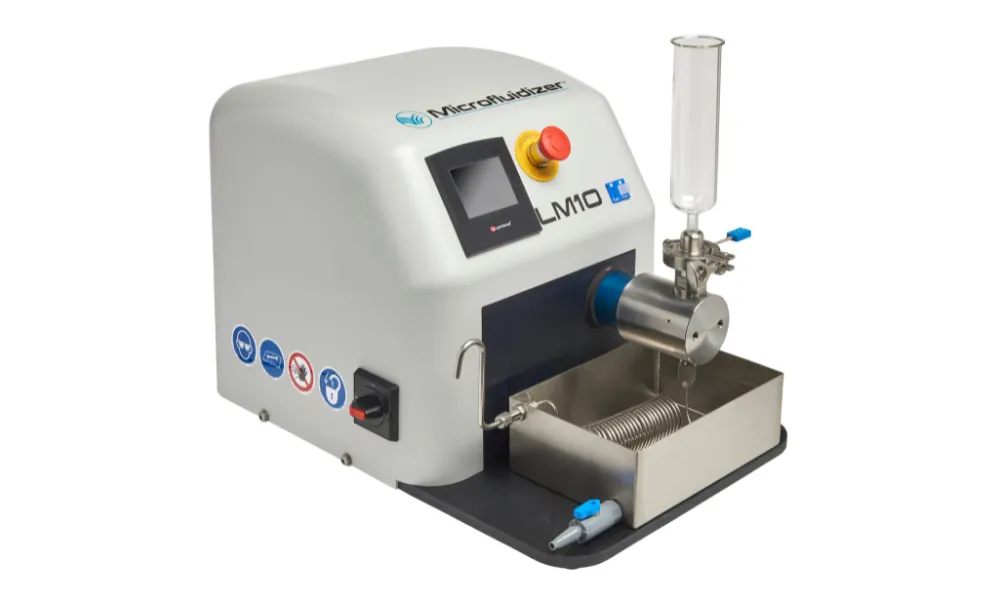
Features
Standard Features
- 300 ml glass reservoir
- Ceramic Interaction Chamber™
- Cooling coil and bath assembly
- Easily autoclavable
- Easy-to-use color touchscreen control interface
- 2 Modes of operation for various compressor sizes
- Calibrate Microfluidizer® processor to specific compressor
Optional Features
- Diamond Interaction Chamber™
- Process pressure transducer
- Larger capacity stainless steel reservoirs
- Thermocouples at product inlet and outlet
- Process fluid recirculation assembly/kit
- Gasket materials
- Auxiliary Processor Module™ (APM™)
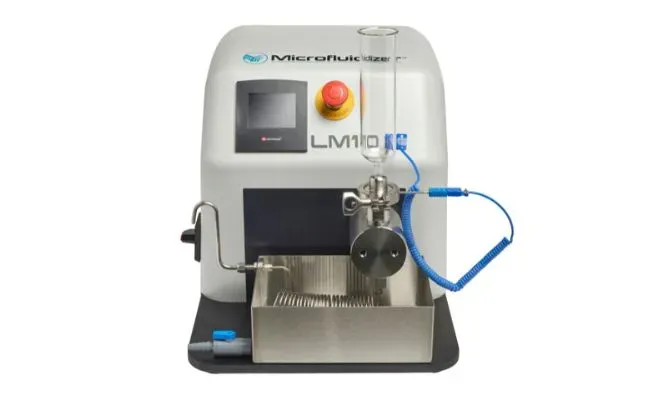
Digitally Controlled Lab Unit for Small Sample Material Processing
- Operates at pressures up to 23,000 psi (1586 bar)
- Requires a minimum sample size of 30 ml
- Achieves unmatched particle size reduction/disruption performance at low process pressure, which limits sample temperature rise during processing
- Attains higher product yields after sterile filtration with tighter particle size distribution
- Promotes optimal temperature control through the removable cooling coil and bath
- Saves on development time in pilot/production with linear volumetric scale-up
- Enhances repeatability with easy-to-use digital pressure control
- Real-time temperature monitoring capability
- Ensures dependable process performance over time with maintenance reminder and operator alerts