The TSR range comprises a split tube furnace horizontally mounted on a base frame, and fitted with a friction drive rotation system, allowing for work tube rotations of up to 10 rpm. The frame can be manually tilted up to a maximum angle of 6˚ to suit the requirements of the material being processed.
Accessory work tubes can easily be exchanged to meet the different physical or chemical requirements of a process.
Optional built-in gas systems enable users to equip the TSR rotating tube furnace for operation under a modified atmosphere.
Max temp
1150 °C
Furnace Ø
125 mm
Heated length(s)
1000 mm
Number of heated zones
1 zone or 3 zones
Orientation
horizontal
LEADING HEAT TECHNOLOGY
Carbolite Gero's new tube furnace range is at the pinnacle of furnace design. The culmination of over 80 years of experience in thermal engineering; combining the latest technological developments with solid construction, high-quality components and a sleek, modern aesthetic.
The rotating motion of the TSR helps increase the surface area of the sample material exposed to the atmosphere within the work tube, helping to speed up reaction times and improve the overall yield. A 5 litre capacity vibratory feeder and corresponding collection hopper makes the TSR the ideal choice for continuous heat treatment processes.
HIGH QUALITY HEATING ELEMENTS
- Excellent temperature uniformity
- Fast heat-up and cool-down rates
- Unsurpassed temperature uniformity along the entire heated length
HIGH QUALITY THERMAL INSULATION
- Low energy consumption
- Low external case temperature
- Designed for longevity
TEMPERATURE CONTROL & COMMUNICATIONS
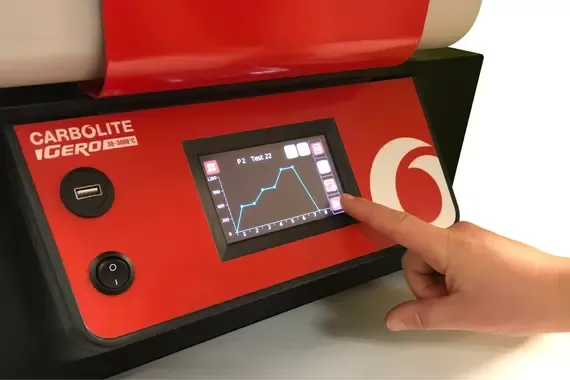
TSR rotating tube furnaces are equipped with ethernet communications and a programmable controller with 24 segments as standard:
- Single zone furnaces fitted with Carbolite Gero EPC3016P1 controller
- Three zone furnaces fitted with Carbolite Gero CC-T1 touch-screen controller
OPTIONS
- Over-temperature protection (recommended to protect valuable contents and for unattended operation)
- A range of sophisticated digital controllers, multi-segment programmers and data loggers is available. These can be fitted with RS232, RS485 or Ethernet communications.
MODIFIED ATMOSPHERE AND MATERIAL MOVEMENT
The Carbolite Gero TSR rotating tube furnace may be equipped with gas connections to accommodate modified atmosphere applications.
The gas system is built into the frame of the furnace and required gases and control method must be specified at time of order. Options include manual flowmeters or digital mass flow controllers.
The TSR is available with a choice of different work tubes. Please note that the maximum operating temperature is dependent on the properties of the work tube material selected.
To accurately control the flow of sample material into the furnace, the TSR is fitted with both a 5 litre hopper and vibratory feeder, as standard. A 5 litre collection hopper with manual discharge valve is also included to safely gather processed material.
OPTIONS
- Gas connection kit to enable operation under modified atmospheres
- Inert gas package modules allow for the use of up to 3 non-reactive gases (available with either manual or automatic control)
- Input hopper with screw feeder
Standard quartz work tube and optional metallic work tube
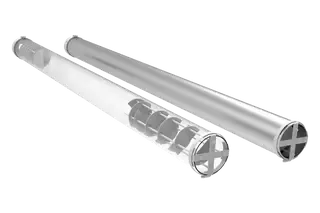
Gas flow control by a digital flow meter
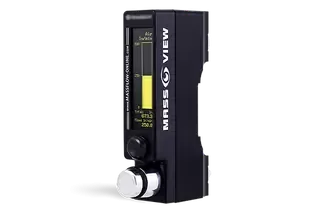
CUSTOM DESIGN OPTIONS
We have a wealth of knowledge built up over years of assisting customers with their rotating tube furnace applications. Certain applications will benefit from a selection of custom options including:
Material movement options to aid movement of the material including:
- Metallic helical work tube inserts. These are used to control the movement of material through the work tube
- Feed knockers and agitators
- Scraper bars or wires within the work tube
- Water cooled collection hopper
- Automated discharge valve
- Steam injection - digitally controlled evaporator/mixer unit with mass flow controllers for the delivery of a carrier gas (N2) and water
ANGLE OF INCLINATION
To assist in the flow of material through the work tube, the TSR can be tilted to a maximum of 6° using the manual winding wheel. By adjusting the angle of inclination, the operator can control the residence time of the material within the heated zone of the rotating tube furnace; the ability to change the angle ensures that the TSR has the flexibility to process many different materials with various grain sizes, from granules to powder.
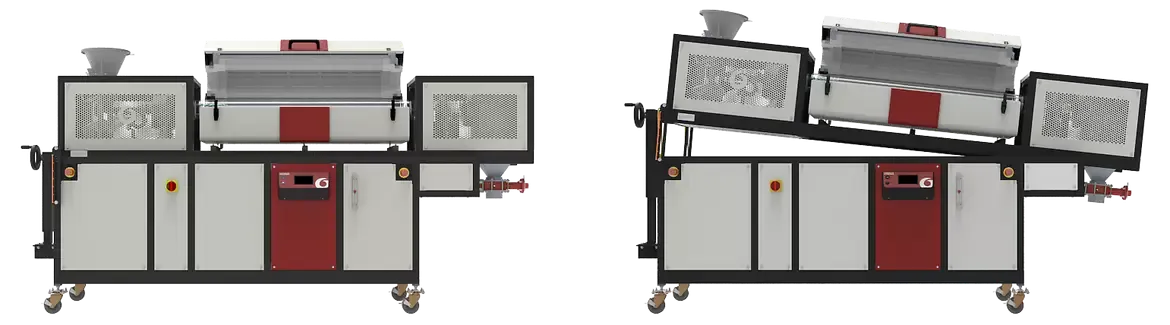
TORREFACTION & BIO-COAL
Torrefaction is a thermochemical process carried out in the absence of oxygen to cause the partial decomposition of biomass. Water and volatiles are released from the biomass to leave a solid, dry material known as bio-coal. For some applications, bio coal can be used to replace traditional fossil fuels, thus helping to reduce CO2 emissions.
In this video, both RETSCH cutting mill SM 300 and the CARBOLITE GERO rotating tube furnace TSR have been used as a part of a torrefaction process to create bio-coal fuel.
The Verder Scientific companies provide solutions to support your process every step of the way, from sample preparation and analysis, to heat treatment, and more.
TECHNICAL DATA
| TSR1 11/125/1000 | TSR3 11/125/1000 |
Max temp (°C) | 1150 | 1150 |
Max. outer diameter accessory tube (mm) | 125 | 125 |
Number of heated zones | 1 | 3 |
Heated length (mm) | 1000 | 1000 |
Work tube length (mm) | 2000 | 2000 |
Dimensions:
External H x W x D (mm) | 1830 x 3150 x 700 | 1830 x 3150 x 700 |
Max power (W) | 3810 | 3810 |
MODEL NAMES EXPLAINED
TSR1 11/125/1000 Number of heated zones: 1 zone or 3 zones
TSR1 11/125/1000 Max temp: 1150 °C
TSR1 11/125/1000 Furnace Ø: 125 mm
TSR1 11/125/1000 Heated length(s): 1000 mm
PLEASE NOTE
- Maximum continuous operating temperature is 1050 °C
- (Max. operating temperature dependent on work tube material)
- All furnaces are equipped with thermocouple type N