Significant properties for cut-off wheels are wear (i.e., abrasion resistance), long lifetime and cutting performance. Characteristics of the wheel composition are the abrasive used (aluminum oxide, silicon carbide, diamond, cubic boron nitride (CBN)) and the bond type (metal, resin or rubber). The goal of any cut is to separate the material with minimal deformation and temperature effect. For a clean cut, the abrasive particles and bond type of the cut-off wheel should be matched to the material being cut.
QPREP Premium cut-off wheels offer the optimal solution for a wide range of applications.
- Achieve a fine cutting surface
- Wide range of cut-off wheels for cutting all materials
- The best cutting function fitting to the material
- Low deformation and temperature during the cutting process
- Very good cutting performance with long lifetime
The color coding of the premium cut-off wheels enables quick, visual assignment and identification of the several types.
CUT-OFF WHEEL SELECTION ACCORDING TO MATERIAL HARDNESS
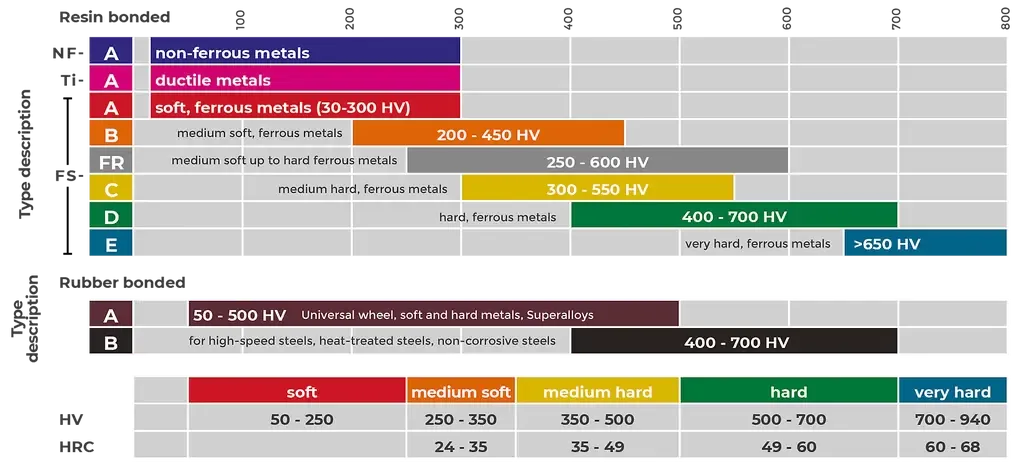
PREMIUM SILICON CARBIDE CUT-OFF WHEEL
BOND: RESIN
Due to the lower hardness of silicon carbide particles compared to aluminum oxide particles, these premium cut-off wheels are the optimal choice for cutting soft as well as non-ferrous materials.
Product Advantages
- Optimized cutting performance for non-ferrous metals and ductile metals
- Long lifetime as well as low wear of the cut-off wheel
Recommended applications
- QPREP Premium Silicon Carbide cut-off wheel NF-A (30-300 HV) are suitable for cutting soft and medium hard non-ferrous metals as well as hard non-metallic materials (glass, stone).
- QPREP Premium Silicon Carbide cut-off wheel Ti-A (30-300 HV) for cutting non-ferrous metals, Ti alloys and refractory metals
PREMIUM ALUMINIUM OXIDE CUT-OFF WHEEL
BOND: RESIN
QPREP Premium Aluminum oxide cut-off wheels cover a wide range of materials from 30 HV to >650 HV.
Product Advantages
- Wide range of application for various materials with different hardness’s
- Long lifetime as well as low wear of the cut-off wheel
- Premium abrasive particles enable the finest cutting surfaces, which shortens the following grinding steps
- The synthetic resin bond allows dull abrasive particles to break out evenly during the cutting process
Recommended applications
- Cutting of all materials
- Cutting of polymers with the hard-bonded cut-off wheel FS-A
- FS-FR low-wear cut-off wheel in the 250 to 600 HV range, especially suitable for manual cutting
- Cutting of very hard steels with the soft-bonded cut-off wheel FS-E
PREMIUM ALUMINIUM OXIDE CUT-OFF WHEEL
BOND: RUBBER
QPREP Premium Aluminum oxide cut-off wheels with rubber bonds cover a wide range of materials from 50 HV to 700 HV and are suitable for soft and hard metals, superalloys (Type A) or high-speed steels, heat-treated steels and non-corrosive steels (Type B)
Recommended applications
- Type A: 50- 500 HV
- Type B: 400- 700 HV
PREMIUM DIAMOND CUT-OFF WHEEL
BOND: RESIN / BRONZE
QPREP Premium Diamond cut-off wheels are used for hard materials (ceramics, glass fiber reinforced plastics, minerals and rocks, glass or similar). There are two different bond variants to choose from: metallic, in which the diamonds are usually bound in a bronze bond, or the bond with synthetic resin.
Product Advantages
- Two different bond types (bronze and resin) for a wide range of applications.
- The dressing function ensures that the diamonds always maintain maximum cutting performance.
- Long lifetime as well as low wear of the cut-off wheel
Recommended applications
- Cutting of ceramic materials as well as composites with bronzebonded diamond premium cut-off wheels
- Cutting of hard and brittle materials with resin-bonded diamond cutting discs
- Cutting of brittle coating surfaces
PREMIUM CBN CUT-OFF WHEEL
BOND: BRONZE
QPREP Premium CBN cut-off wheels made of cubic boron nitride provide a fine cutting surface for nickel and cobaltbased alloys. The high hardness as well as the high ductility of the CBN particles improve the cutting ability of the cut-off wheel with significantly less wear. The CBN abrasives in these discs maintain cutting performance over a longer period, which improves the cutting ability of the cut-off wheels.
Product Advantages
- The good thermal conductivity of CBN abrasives can dissipate heat generated during cutting much more effectively
- Long lifetime as well as low wear of the cut-off wheel
- The dressing function ensures that the CBN particles always maintain the highest cutting performance
Recommended applications
- For the cutting of composite materials
- For cutting very hard steels
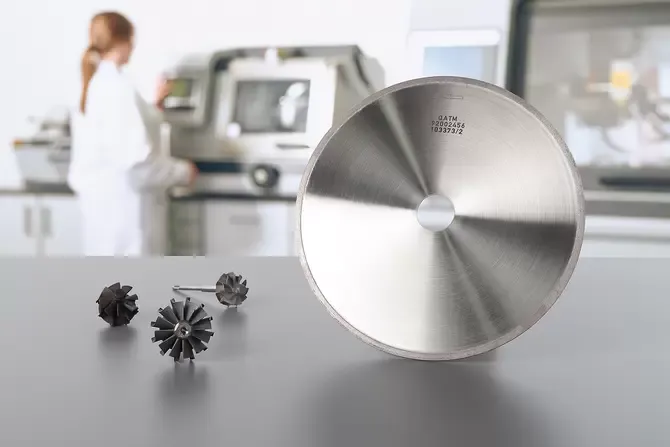