Electrically Powered High Shear Lab-Scale Unit
The LM20 Microfluidizer high-pressure processor ensures that 100% of your material undergoes exactly the same treatment, yielding consistently reliable results that include uniform particle and droplet size reduction, submicron emulsions and high-yield cell disruption.
Our unique design converts pressure into shear forces more efficiently than other technologies, delivering superior performance. The LM20’s unique intensifier pump supplies the desired pressure at a constant rate to your materials, driving them through precisely defined, fixed-geometry microchannels within the Interaction Chamber™. The product stream accelerates to high velocities, creating shear rates that are orders of magnitude greater than any other conventional method.
The LM20 Microfluidizer® benchtop homogenizer can easily and linearly be scaled up to larger volumes. By operating under the same conditions, our LM20 Microfluidizer® processor can seamlessly achieve consistent, reliable results on the pilot and production models.
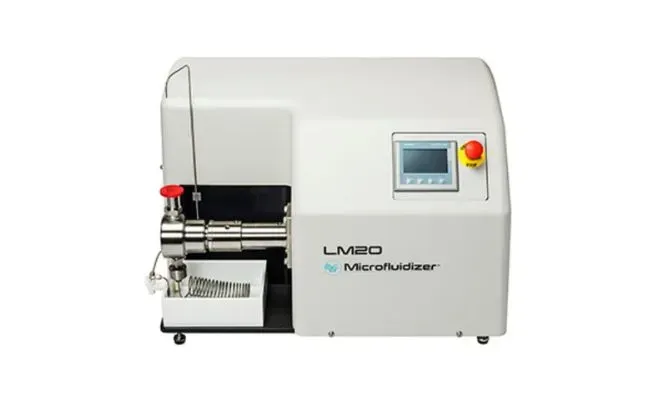
Standard Features
- 300 ml glass reservoir
- Diamond Interaction Chamber™ (ceramic chamber is standard on LM20-20 model)
- Digital pressure control
- Integrated stroke counter with maintenance reminder
- Multiple languages (selectable by user)
Optional Features
- Auxiliary Processing Module™ (APM™)
- Cooling coil, bath & recirculation assembly
- Process pressure gauge
- Larger capacity stainless steel reservoirs
- Solvent-resistant gasket materials
- Seal quench fittings
- Nitrogen adapter assembly
Benefits
Like all Microfluidizer® processors, the digitally controlled LM20 excels at efficiently converting high fluid pressures to intense shear forces.
- Requires a minimum sample size of 14 ml.
- Is suitable for laboratory and benchtop applications.
- Achieves unmatched particle/droplet size reduction/disruption performance at lower process pressure.
- Limits sample temperature rise during processing, ensuring minimal heat denaturation of sensitive materials.
- Results in higher product yields after sterile filtration with tighter particle size distribution.
- Saves on development time in pilot/production scale with linear volumetric scale-up.
- Provides enhanced repeatability with easy-to-use digital pressure control.
- Incorporates a compact design that fits in a fume hood.
- Ensures dependable process performance over time with maintenance reminder and operator alerts.
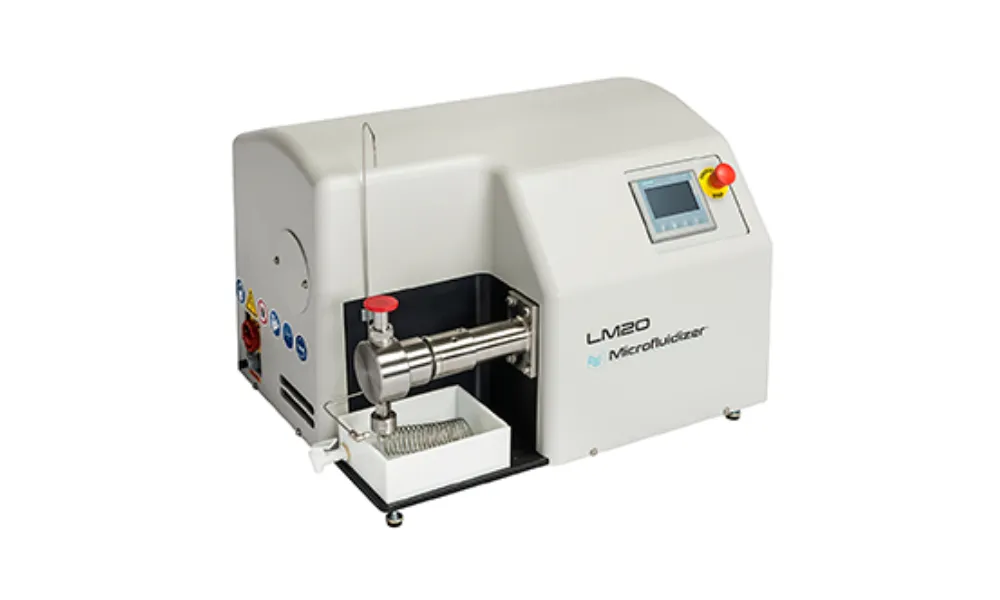